
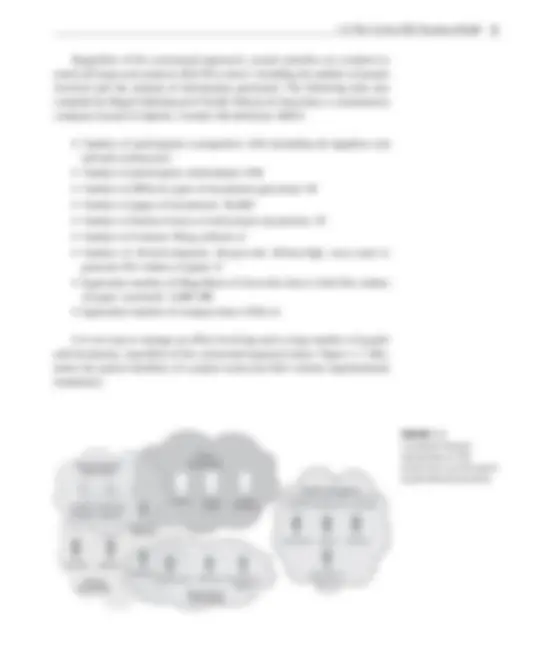
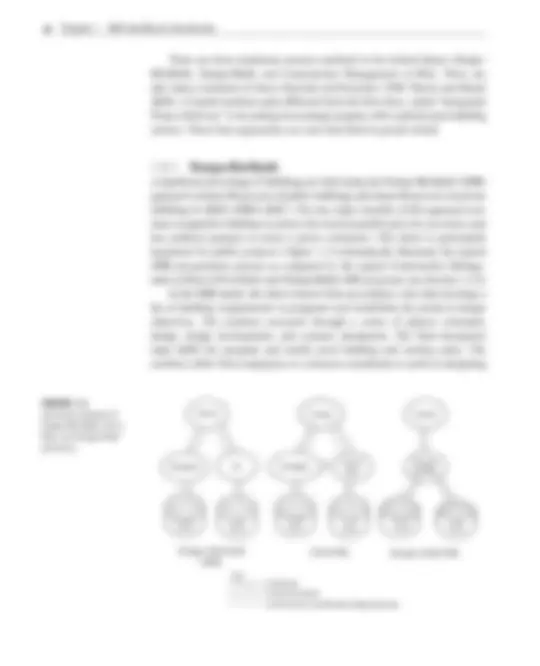
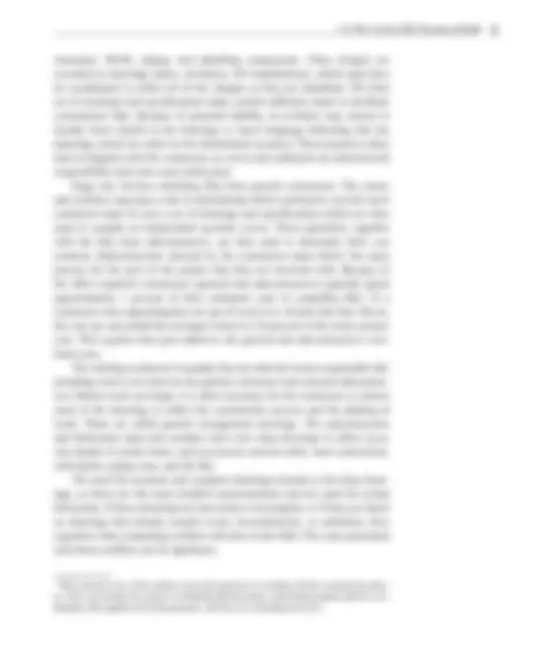
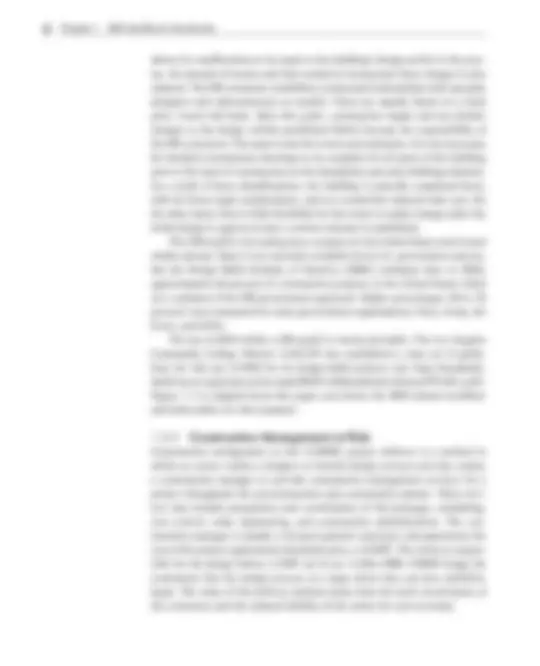
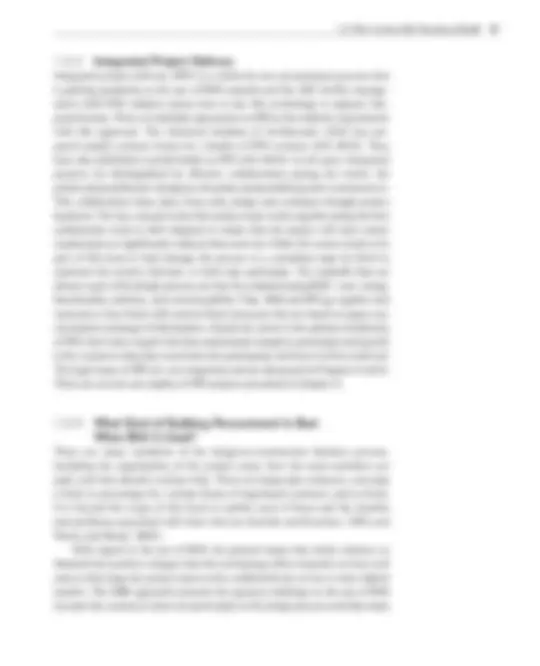
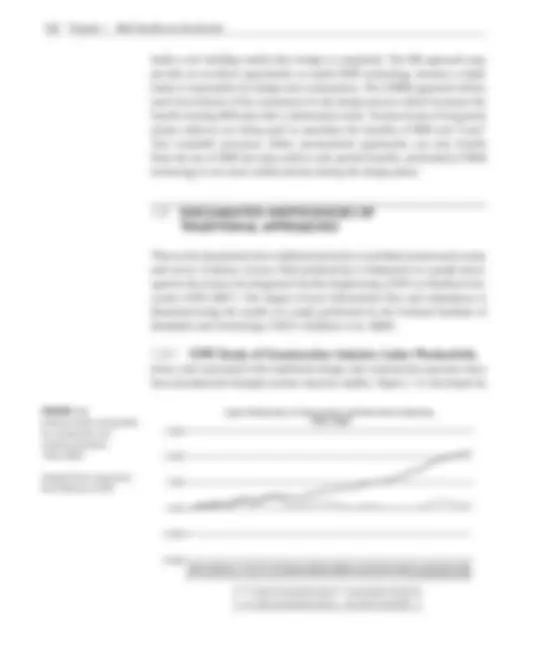
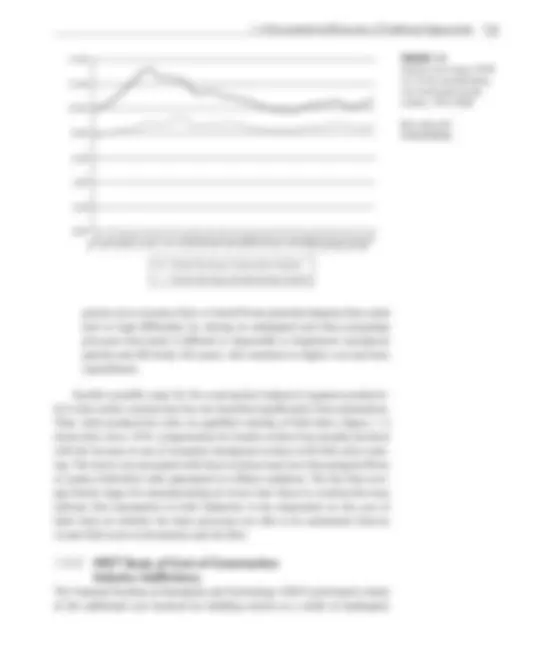
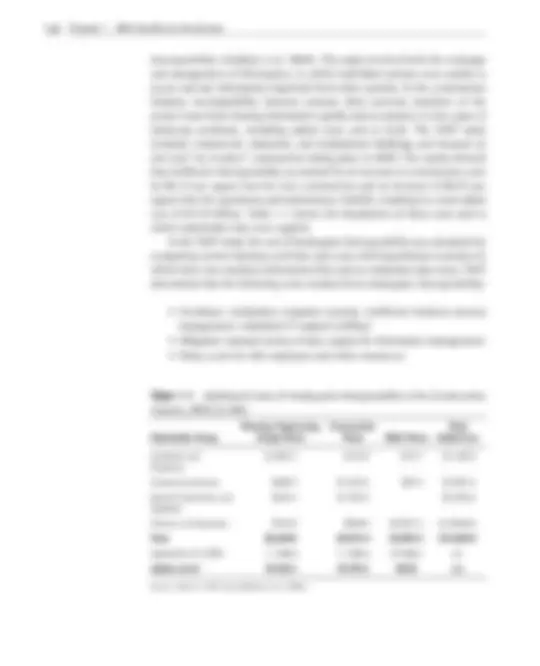
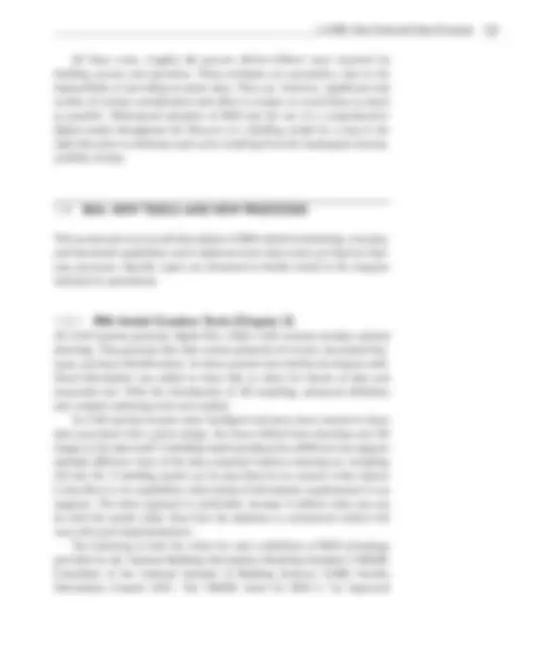
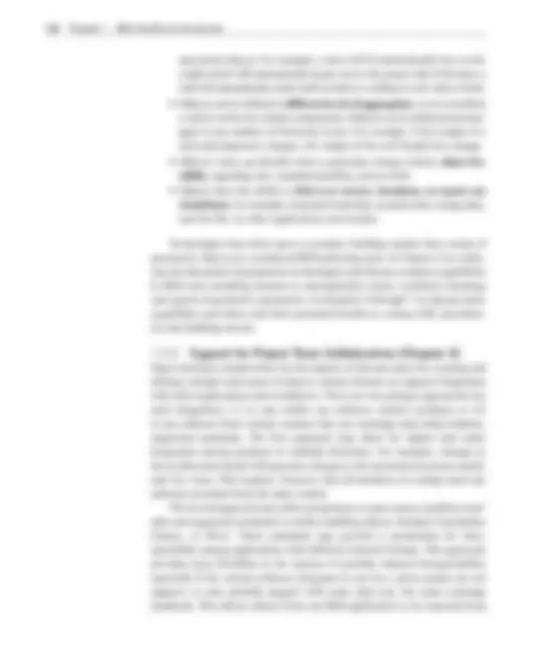
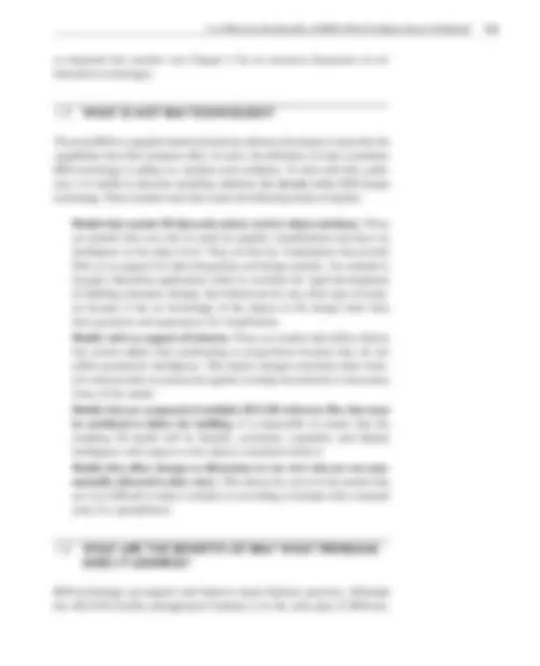
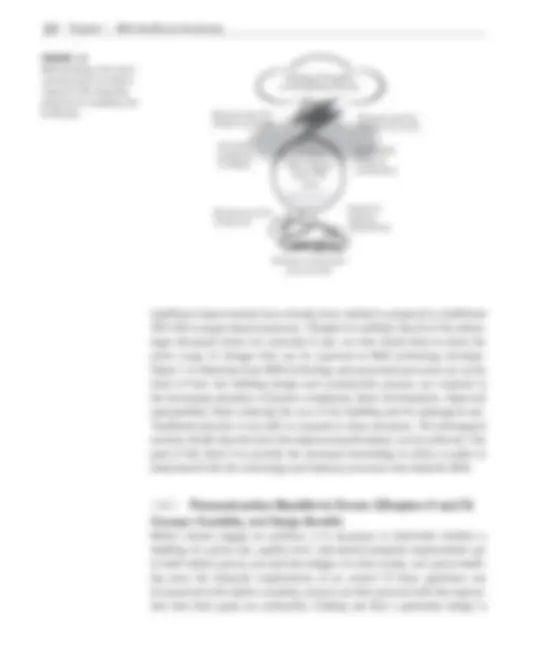
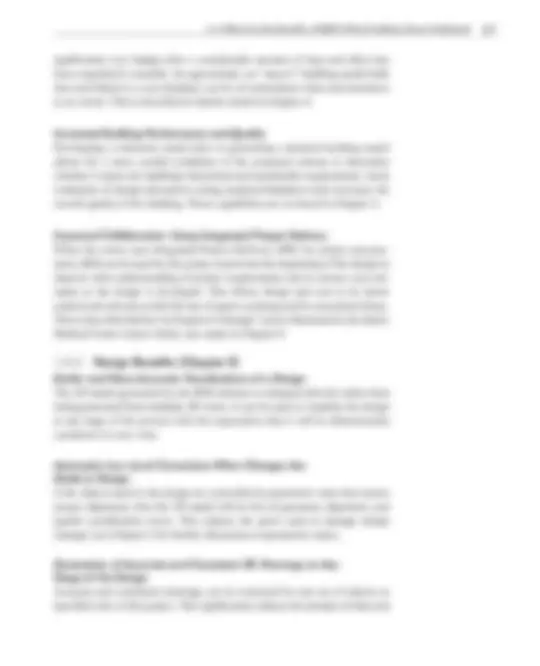
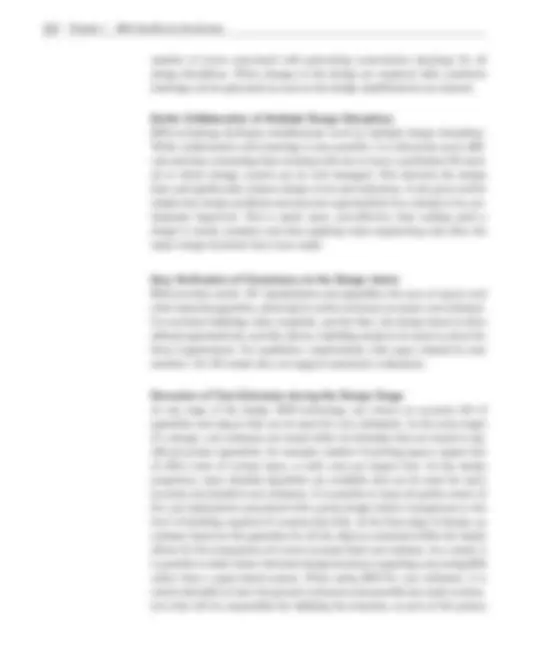
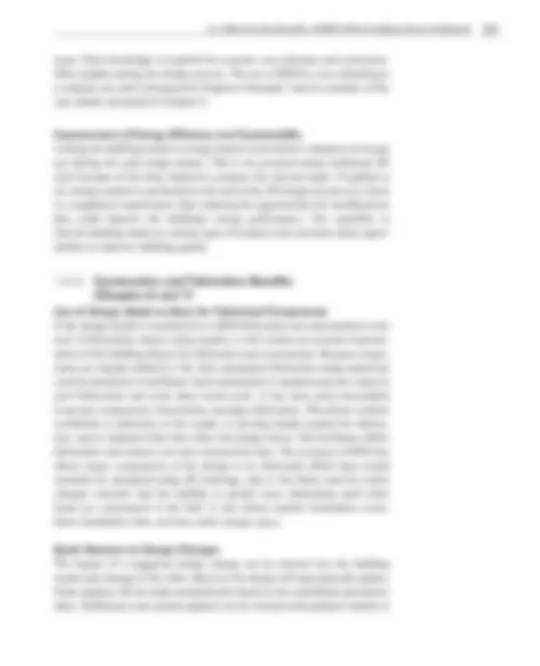
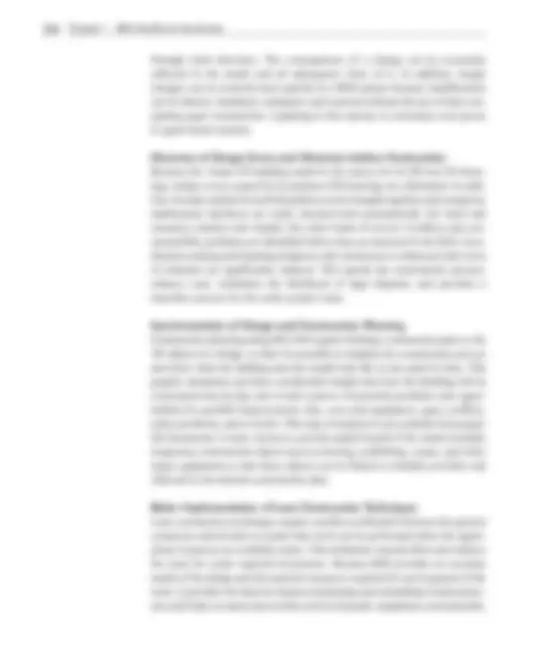
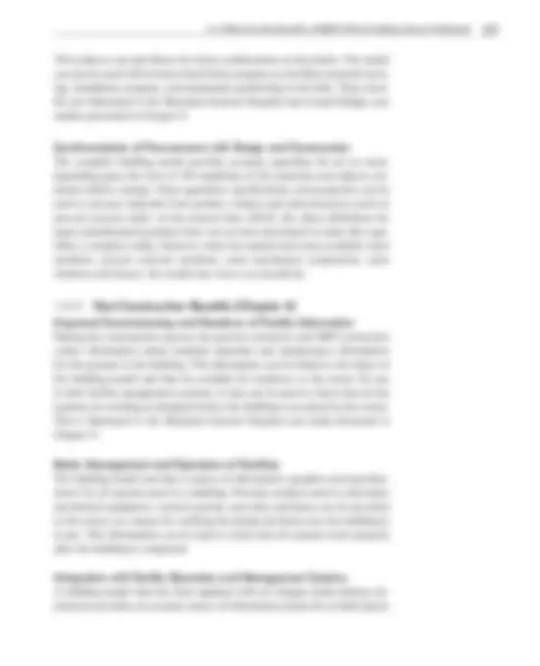
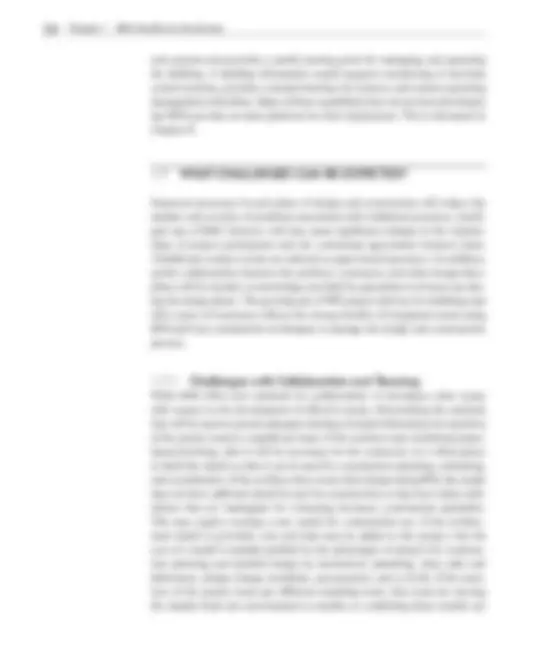
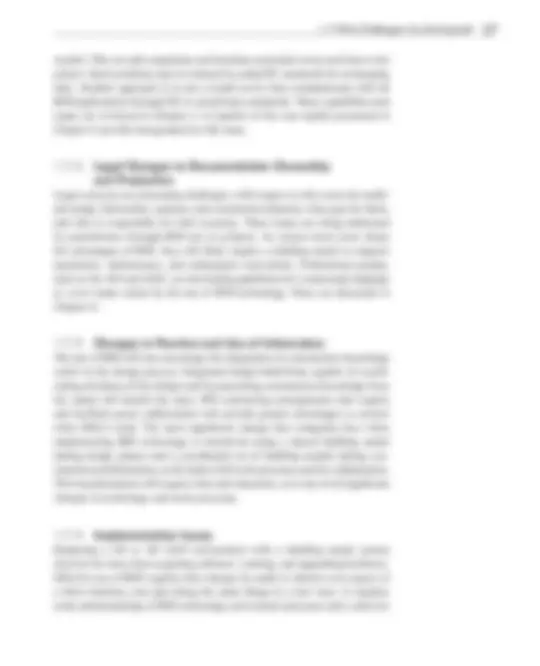
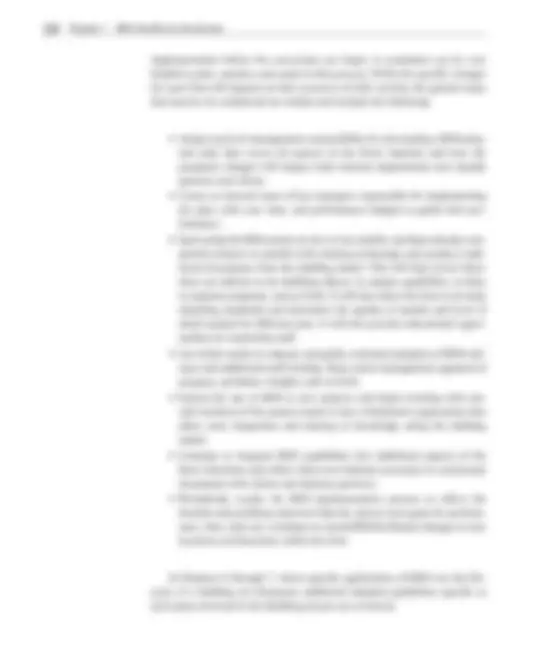
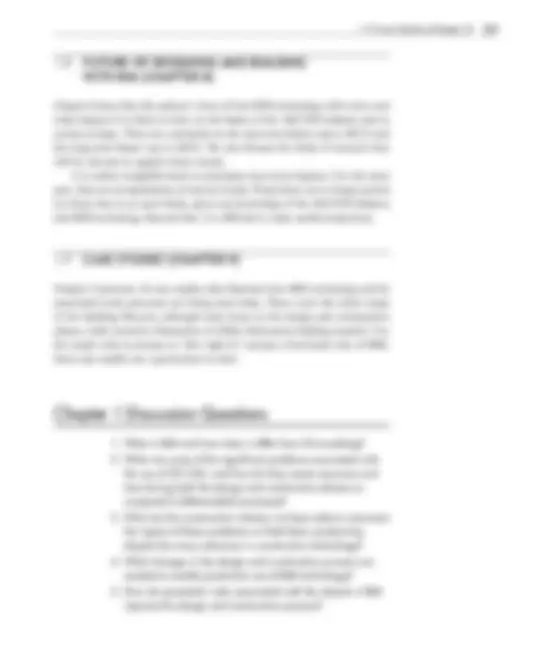
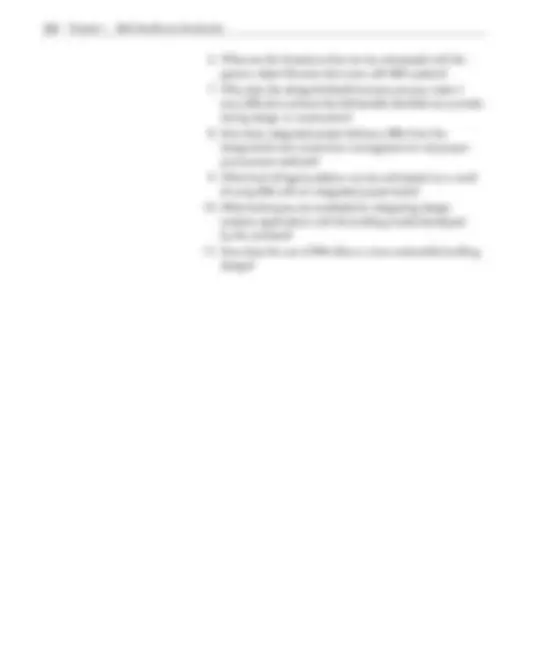
Study with the several resources on Docsity
Earn points by helping other students or get them with a premium plan
Prepare for your exams
Study with the several resources on Docsity
Earn points to download
Earn points by helping other students or get them with a premium plan
Community
Ask the community for help and clear up your study doubts
Discover the best universities in your country according to Docsity users
Free resources
Download our free guides on studying techniques, anxiety management strategies, and thesis advice from Docsity tutors
Building information modeling (bim), a technology and set of processes used in the aec/fm industry for planning, designing, constructing, and maintaining buildings. Bim facilitates better collaboration, improved sustainability, reduced costs, and increased efficiency. The benefits of bim, design-build and construction management at risk approaches, and challenges in implementing bim.
What you will learn
Typology: Study Guides, Projects, Research
1 / 30
This page cannot be seen from the preview
Don't miss anything!
Building Information Modeling (BIM) is one of the most promising develop- ments in the architecture, engineering, and construction (AEC) industries. With BIM technology, one or more accurate virtual models of a building are constructed digitally. They support design through its phases, allowing better analysis and control than manual processes. When completed, these computer- generated models contain precise geometry and data needed to support the construction, fabrication, and procurement activities through which the building is realized. BIM also accommodates many of the functions needed to model the lifecycle of a building, providing the basis for new design and construction capabilities and changes in the roles and relationships among a project team. When adopted well, BIM facilitates a more integrated design and construction process that results in better quality buildings at lower cost and reduced project duration. This chapter begins with a description of existing construction practices, and it documents the inefficiencies inherent in these methods. It then explains
1
2 Chapter 1^ BIM Handbook Introduction
both the technology behind BIM and recommends ways to best take advantage of the new business processes it enables for the entire lifecycle of a building. It concludes with an appraisal of various problems one might encounter when converting to BIM technology.
To better understand the significant changes that BIM introduces, this chapter begins with a description of current paper-based design and construction meth- ods and the predominant business models now in use by the construction industry. It then describes various problems associated with these practices, out- lines what BIM is, and explains how it differs from 2D and 3D computer-aided design (CAD). We give a brief description of the kinds of problems that BIM can solve and the new business models that it enables. The chapter concludes with a presentation of the most significant problems that may arise when using the technology, which is now only in its early phase of development and use.
Currently, the facility delivery process remains fragmented, and it depends on paper-based modes of communication. Errors and omissions in paper docu- ments often cause unanticipated field costs, delays, and eventual lawsuits between the various parties in a project team. These problems cause friction, fi nancial expense, and delays. Efforts to address such problems have included: alternative organizational structures such as the design-build method; the use of real-time technology, such as project Web sites for sharing plans and docu- ments; and the implementation of 3D CAD tools. Though these methods have improved the timely exchange of information, they have done little to reduce the severity and frequency of conflicts caused by paper documents or their electronic equivalents. One of the most common problems associated with 2D-based communi- cation during the design phase is the considerable time and expense required to generate critical assessment information about a proposed design, includ- ing cost estimates, energy-use analysis, structural details, and so forth. These analyses are normally done last, when it is already too late to make impor- tant changes. Because these iterative improvements do not happen during the design phase, value engineering must then be undertaken to address inconsist- encies, which often results in compromises to the original design.
4 Chapter 1^ BIM Handbook Introduction
There are three dominant contract methods in the United States: Design- Bid-Build, Design-Build, and Construction Management at Risk. There are also many variations of these (Sanvido and Konchar 1999; Warne and Beard 2005). A fourth method, quite different from the first three, called “Integrated Project Delivery” is becoming increasingly popular with sophisticated building owners. These four approaches are now described in greater detail.
A significant percentage of buildings are built using the Design-Bid-Build (DBB) approach (almost 90 percent of public buildings and about 40 percent of private buildings in 2002) (DBIA 2007). The two major benefits of this approach are: more competitive bidding to achieve the lowest possible price for an owner; and less political pressure to select a given contractor. (The latter is particularly important for public projects.) Figure 1–2 schematically illustrates the typical DBB procurement process as compared to the typical Construction Manage- ment at Risk (CM at Risk) and Design-Build (DB) processes (see Section 1.2.2) In the DBB model, the client (owner) hires an architect, who then develops a list of building requirements (a program) and establishes the project’s design objectives. The architect proceeds through a series of phases: schematic design, design development, and contract documents. The final documents must fulfill the program and satisfy local building and zoning codes. The architect either hires employees or contracts consultants to assist in designing
FIGURE 1– Schematic diagram of Design-Bid-Build, CM at Risk, and Design-Build processes.
Owner
CM at Designer GC Designer Risk Design Builder
Owner Owner
Design Subs
Trade Subs
Design Subs
Trade Subs
Design Subs
Trade Subs
key Contracts Communication Contractual Coordination Requirements
Design–Bid–Build (DBB)
CM at Risk (^) Design–Build (DB)
1.2 The Current AEC Business Model (^5)
structural, HVAC, piping, and plumbing components. These designs are recorded on drawings (plans, elevations, 3D visualizations), which must then be coordinated to reflect all of the changes as they are identified. The final set of drawings and specifications must contain sufficient detail to facilitate construction bids. Because of potential liability, an architect may choose to include fewer details in the drawings or insert language indicating that the drawings cannot be relied on for dimensional accuracy. These practices often lead to disputes with the contractor, as errors and omissions are detected and responsibility and extra costs reallocated. Stage two involves obtaining bids from general contractors. The owner and architect may play a role in determining which contractors can bid. Each contractor must be sent a set of drawings and specifications which are then used to compile an independent quantity survey. These quantities, together with the bids from subcontractors, are then used to determine their cost estimate. Subcontractors selected by the contractors must follow the same process for the part of the project that they are involved with. Because of the effort required, contractors (general and subcontractors) typically spend approximately 1 percent of their estimated costs in compiling bids.^1 If a contractor wins approximately one out of every 6 to 10 jobs that they bid on, the cost per successful bid averages from 6 to 10 percent of the entire project cost. This expense then gets added to the general and subcontractors’ over- head costs. The winning contractor is usually the one with the lowest responsible bid, including work to be done by the general contractor and selected subcontrac- tors. Before work can begin, it is often necessary for the contractor to redraw some of the drawings to reflect the construction process and the phasing of work. These are called general arrangement drawings. The subcontractors and fabricators must also produce their own shop drawings to reflect accu- rate details of certain items, such as precast concrete units, steel connections, wall details, piping runs, and the like. The need for accurate and complete drawings extends to the shop draw- ings, as these are the most detailed representations and are used for actual fabrication. If these drawings are inaccurate or incomplete, or if they are based on drawings that already contain errors, inconsistencies, or omissions, then expensive time-consuming conflicts will arise in the field. The costs associated with these conflicts can be signifi cant.
(^1) This is based on two of the authors’ personal experience in working with the construction indus- try. This cost includes the expense of obtaining bid documents, performing quantity takeoff, coor- dinating with suppliers and subcontractors, and the cost estimating processes.
1.2 The Current AEC Business Model (^7)
As a result of these problems, the DBB approach is probably not the most expeditious or cost-efficient approach to design and construction. Other approaches have been developed to address these problems.
The design-build (DB) process was developed to consolidate responsibility for design and construction into a single contracting entity and to simplify the administration of tasks for the owner (Beard et al. 2005). Figure 1–3 illustrates this process. In this model, the owner contracts directly with the design-build team (normally a contractor with a design capability or working with an architect) to develop a well-defined building program and a schematic design that meets the owner’s needs. The DB contractor then estimates the total cost and time needed to design and construct the building. After all modifications requested by the owner are implemented, the plan is approved and the final budget for the project is established. It is important to note that because the DB model
Capture Program Requirements Excel
Revit Sketchup
3D Rendering MEP System Development
Program Validation
Building System Modeling
Material Schedules
Revit, 3D Max Revit
Animation Walkthru
3D Max
System Prototyping
Design Bid Documents
Specifica- tions
E-Specs Submittal Review & Doc. in BIM
BIM Storm
RFI Response, Design Change Documentation
Programming and Pre- Design
Competitive Evaluation Process
Design Phase
Construction
Operations
Revit, 3D Max
Revit, 3D Max Revit, Excel Revit
Revit, Civil, 3D, Bentley, Projectwise? Revit, Projectwise?
Revit, Autocad, MEP, Civil, 3D Max
FIGURE 1– Adapted from workflow and deliverables for LACCD BIM standard on design- build projects (only the BIM-related workflows are shown).
8 Chapter 1^ BIM Handbook Introduction
allows for modifications to be made to the building’s design earlier in the proc- ess, the amount of money and time needed to incorporate these changes is also reduced. The DB contractor establishes contractual relationships with specialty designers and subcontractors as needed. These are usually based on a fixed price, lowest bid basis. After this point, construction begins and any further changes to the design (within predefined limits) become the responsibility of the DB contractor. The same is true for errors and omissions. It is not necessary for detailed construction drawings to be complete for all parts of the building prior to the start of construction on the foundation and early building elements. As a result of these simplifications, the building is typically completed faster, with far fewer legal complications, and at a somewhat reduced total cost. On the other hand, there is little flexibility for the owner to make changes after the initial design is approved and a contract amount is established. The DB model is becoming more common in the United States and is used widely abroad. Data is not currently available from U.S. government sources, but the Design Build Institute of America (DBIA) estimates that, in 2006, approximately 40 percent of construction projects in the United States relied on a variation of the DB procurement approach. Higher percentages (50 to 70 percent) were measured for some government organizations (Navy, Army, Air Force, and GSA). The use of BIM within a DB model is clearly advisable. The Los Angeles Community College District (LACCD) has established a clear set of guide- lines for this use of BIM for its design-build projects (see http://standards. build-laccd.org/projects/dcs/pub/BIM%20Standards/released/PV-001.pdf). Figure 1–3 is adapted from this paper and shows the BIM-related workflow and deliverables for this standard.
Construction management at risk (CM@R) project delivery is a method in which an owner retains a designer to furnish design services and also retains a construction manager to provide construction management services for a project throughout the preconstruction and construction phases. These serv- ices may include preparation and coordination of bid packages, scheduling, cost control, value engineering, and construction administration. The con- struction manager is usually a licensed general contractor and guarantees the cost of the project (guaranteed maximum price, or GMP). The owner is respon- sible for the design before a GMP can be set. Unlike DBB, CM@R brings the constructor into the design process at a stage where they can have definitive input. The value of the delivery method stems from the early involvement of the contractor and the reduced liability of the owner for cost overruns.
build a new building model after design is completed. The DB approach may provide an excellent opportunity to exploit BIM technology, because a single entity is responsible for design and construction. The CM@R approach allows early involvement of the constructor in the design process which increases the benefi t of using BIM and other collaboration tools. Various forms of integrated project delivery are being used to maximize the benefits of BIM and “Lean” (less wasteful) processes. Other procurement approaches can also benefit from the use of BIM but may achieve only partial benefits, particularly if BIM technology is not used collaboratively during the design phase.
This section documents how traditional practices contribute unnecessary waste and errors. Evidence of poor field productivity is illustrated in a graph devel- oped by the Center for Integrated Facility Engineering (CIFE) at Stanford Uni- versity (CIFE 2007). The impact of poor information flow and redundancy is illustrated using the results of a study performed by the National Institute of Standards and Technology (NIST) (Gallaher et al. 2004).
Extra costs associated with traditional design and construction practices have been documented through various research studies. Figure 1–4, developed by
Labor Productivity in Construction and Non-Farm Industries, 1964–
1964196519661967196819691970197119721973197419751976197719781979198019811982198319841985198619871988198919901991199219931994199519961997199819992000200120022003200420052006200720082009 Labor productivity factor – construction industry Labor productivity factor – non-farm industries
FIGURE 1– Indexes of labor productivity for construction and nonfarm industries, 1964–2009.
Adapted from research by Paul Teicholz at CIFE.
10 Chapter 1^ BIM Handbook Introduction
one of the authors, illustrates productivity within the U.S. field construction industry relative to all nonfarm industries over a period of 45 years, from 1964 through 2009. The data was calculated by dividing constant contract dollars (from the Department of Commerce) by field worker-hours of labor for those contracts (from the Bureau of Labor Statistics). These contracts include archi- tectural and engineering costs as well as cost for materials and for the delivery of offsite components to the site. Costs associated with the installation of heavy production equipment, such as printing presses, stamping machines, and the like, are not included. The amount of worker-hours required for labor excludes offsite work, such as steel fabrication, precast concrete, and so forth, but does include the installation labor for these materials. During this 44-year-long period, the productivity of nonfarm industries (including construction) has more than doubled. Meanwhile, labor productivity within the construction industry is relatively unchanged and is now estimated to be about 10 percent less than what it was in 1964. Labor represents about 40 to 60 percent of con- struction’s estimated costs (depending on the type of structure). Owners were actually paying approximately 5 percent more in 2009 than they would have paid for the same building in 1964. Of course, many material and technologi- cal improvements have been made to buildings in the last four decades. The results are perhaps better than they appear, because quality has increased sub- stantially and offsite prefabrication is becoming a bigger factor. On the other hand, manufactured products are also more complex than they used to be, but they now can be produced at significantly lower cost. The replacement of man- ual labor with automated equipment has resulted in lower labor costs and increased quality. But the same cannot be said for construction practices con- sidering the industry as a whole. Contractors have made greater use of offsite components which take advantage of factory conditions and specialized equipment. Clearly this has allowed for higher quality and lower cost production of components, as com- pared to onsite work (Eastman and Sacks 2008). Although the cost of these components is included in our construction cost data, the labor is not. This tends to make onsite construction productivity appear better than it actually is. The extent of this error, however, is difficult to evaluate because the total cost of offsite production is not well-documented over the total period covered by these statistics.^2
(^2) From 1997–2008 the cost of prefabricated wood and steel components represented about 3. percent of total construction value put in place or about 9.7 percent of the value of the material, supplies, and fuel used for construction (from Economic Census data).
1.3 Documented Inefficiencies of Traditional Approaches (^11)
partner acts to protect him- or herself from potential disputes that could lead to legal diffi culties by relying on antiquated and time-consuming processes that make it diffi cult or impossible to implement resolutions quickly and efficiently. Of course, this translates to higher cost and time expenditures.
Another possible cause for the construction industry’s stagnant productiv- ity is that onsite construction has not benefited significantly from automation. Thus, fi eld productivity relies on qualified training of field labor. Figure 1– shows that, since 1974, compensation for hourly workers has steadily declined with the increase in use of nonunion immigrant workers with little prior train- ing. The lower cost associated with these workers may have discouraged efforts to replace fi eld labor with automated (or offsite) solutions. The fact that aver- age hourly wages for manufacturing are lower than those in construction may indicate that automation in both industries is less dependent on the cost of labor than on whether the basic processes are able to be automated (factory versus field work environments and the like).
The National Institute of Standards and Technology (NIST) performed a study of the additional cost incurred by building owners as a result of inadequate
19641966196819701972197419761978198019821984198619881990199219941996199820002002200420062008 Hourly Earnings–Construction Industry Hourly Earnings–Manufacturing Industry
FIGURE 1– Trends in real wages ( U.S. $) for manufacturing and construction hourly workers, 1974–2008.
BLS, Series ID: EES00500006.
1.3 Documented Inefficiencies of Traditional Approaches (^13)
interoperability (Gallaher et al. 2004). The study involved both the exchange and management of information, in which individual systems were unable to access and use information imported from other systems. In the construction industry, incompatibility between systems often prevents members of the project team from sharing information rapidly and accurately; it is the cause of numerous problems, including added costs, and so forth. The NIST study included commercial, industrial, and institutional buildings and focused on new and “set in place” construction taking place in 2002. The results showed that inefficient interoperability accounted for an increase in construction costs by $6.12 per square foot for new construction and an increase in $0.23 per square foot for operations and maintenance (O&M), resulting in a total added cost of $15.8 billion. Table 1–1 shows the breakdown of these costs and to which stakeholder they were applied. In the NIST study, the cost of inadequate interoperability was calculated by comparing current business activities and costs with hypothetical scenarios in which there was seamless information flow and no redundant data entry. NIST determined that the following costs resulted from inadequate interoperability:
Avoidance (redundant computer systems, inefficient business process management, redundant IT support staffing) Mitigation (manual reentry of data, request for information management) Delay (costs for idle employees and other resources)
Table 1–1 Additional Costs of Inadequate Interoperability in the Construction Industry, 2002 (In $M)
Stakeholder Group
Planning, Engineering, Design Phase
Construction Phase O&M Phase
Total Added Cost Architects and Engineers
$1,007.2 $147.0 $15.7 $1,169.
General Contractors $485.9 $1,265.3 $50.4 $1,801. Special Contractors and Suppliers
$442.4 $1,762.2 $2,204.
Owners and Operators $722.8 $898.0 $9,027.2 $1,0648. Total $2,658.3 $4,072.4 $9,093.3 $15,824. Applicable sf in 2002 1.1 billion 1.1 billion 39 billion n/a Added cost/sf $2.42/sf $3.70/sf $0.23 n/a Source: Table 6.1 NIST study (Gallaher et al. 2004).
14 Chapter 1^ BIM Handbook Introduction
planning, design, construction, operation, and maintenance process using a standardized machine-readable information model for each facility, new or old, which contains all appropriate information created or gathered about that facility in a format useable by all throughout its lifecycle.” (NIBS 2008). The scope of BIM directly or indirectly affects all stakeholders supporting the capital facilities industry. BIM is a fundamentally different way of creating, using, and sharing building lifecycle data. The terms Building Information Model and Building Information Modeling are often used interchangeably, reflecting the term’s growth to manage the expanding needs of the constituency. The NBIMS Initiative categorizes the Building Information Model (BIM) three ways:
1. As a product 2. As an IT-enabled, open standards–based deliverable, and a collaborative process 3. As a facility lifecycle management requirement.
These categories support the creation of the industry information value chain, which is the ultimate evolution of BIM. This enterprise-level (industry- wide) scope of BIM is the area of focus for NBIMS, bringing together the various BIM implementation activities within stakeholder communities.
For the purpose of this book, we define BIM as a modeling technology and associated set of processes to produce, communicate, and analyze building models. Building models are characterized by:
Building components that are represented with digital representa- tions (objects) that carry computable graphic and data attributes that identify them to software applications, as well as parametric rules that allow them to be manipulated in an intelligent fashion. Components that include data that describe how they behave, as needed for analyses and work processes, for example, takeoff, specification, and energy analysis. Consistent and nonredundant data such that changes to component data are represented in all views of the component and the assemblies of which it is a part. Coordinated data such that all views of a model are represented in a coordinated way.
16 Chapter 1^ BIM Handbook Introduction
The methodologies used by NBIMS are rooted in the activities of the International Alliance for Interoperability (IAI), the Information Delivery Manuals (IDM) and Model View Definitions (MVDs), Industry Foundation Dictionaries (IFD), and the development of North American (NA) Information Exchanges that define user requirements and localized content supporting the NA approach to the various building lifecycle processes. BIM supports a reevaluation of IT use in the creation and management of the facility’s lifecycle. The stakeholders include real estate; ownership; finance; all areas of architecture, engineering, and construction (AEC); manufacturing and fabrication; facility maintenance, operations, and planning; regulatory com- pliance; management; sustainment; and disposal within the facility lifecycle. With society’s growing environmental, sustainment, and security mandates, the need for open and reusable critical infrastructure data has grown beyond the needs of those currently supplying services and products to the industry. First- responders, government agencies, and other organizations also need this data. BIM moves the industry forward from current task automation of project and paper-centric processes (3D CAD, animation, linked databases, spread- sheets, and 2D CAD drawings) toward an integrated and interoperable work- flow where these tasks are collapsed into a coordinated and collaborative process that maximizes computing capabilities, Web communication, and data aggregation into information and knowledge capture. All of this is used to sim- ulate and manipulate reality-based models to manage the built environment within a fact-based, repeatable and verifiable decision process that reduces risk and enhances the quality of actions and product industry-wide. The list in the following section is intended to provide a starting point for evaluating specific BIM software tools. See Chapter 2 for more detailed infor- mation about BIM technology and an analysis of current BIM tools.
The concept of parametric objects is central to understanding BIM and its dif- ferentiation from traditional 3D objects. Parametric BIM objects are defined as follows:
Consist of geometric definitions and associated data and rules. Geometry is integrated nonredundantly , and allows for no inconsistencies. When an object is shown in 3D, the shape cannot be represented internally redundantly, for example, as multiple 2D views. A plan and elevation of a given object must always be consistent. Dimensions cannot be “fudged.” Parametric rules for objects automatically modify associated geometries when inserted into a building model or when changes are made to
1.4 BIM: New Tools and New Processes (^17)
or imported into another (see Chapter 3 for an extensive discussion of col- laboration technology).
The term BIM is a popular buzzword used by software developers to describe the capabilities that their products offer. As such, the definition of what constitutes BIM technology is subject to variation and confusion. To deal with this confu- sion, it is useful to describe modeling solutions that do not utilize BIM design technology. These include tools that create the following kinds of models:
Models that contain 3D data only and no (or few) object attributes. These are models that can only be used for graphic visualizations and have no intelligence at the object level. They are fine for visualization but provide little or no support for data integration and design analysis. An example is Google’s SketchUp application which is excellent for rapid development of building schematic designs, but limited use for any other type of analy- sis because it has no knowledge of the objects in the design other than their geometry and appearance for visualization. Models with no support of behavior. These are models that define objects but cannot adjust their positioning or proportions because they do not utilize parametric intelligence. This makes changes extremely labor inten- sive and provides no protection against creating inconsistent or inaccurate views of the model. Models that are composed of multiple 2D CAD reference files that must be combined to define the building. It is impossible to ensure that the resulting 3D model will be feasible, consistent, countable, and display intelligence with respect to the objects contained within it. Models that allow changes to dimensions in one view that are not auto- matically reflected in other views. This allows for errors in the model that are very difficult to detect (similar to overriding a formula with a manual entry in a spreadsheet).
BIM technology can support and improve many business practices. Although the AEC/FM (facility management) industry is in the early days of BIM use,
1.6 What Are the Benefits of BIM? What Problems Does It Address? (^19)
significant improvements have already been realized (compared to traditional 2D CAD or paper-based practices). Though it is unlikely that all of the advan- tages discussed below are currently in use, we have listed them to show the entire scope of changes that can be expected as BIM technology develops. Figure 1–6 illustrates how BIM technology and associated processes are at the heart of how the building design and construction process can respond to the increasing pressures of greater complexity, faster development, improved sustainability while reducing the cost of the building and its subsequent use. Traditional practice is not able to respond to these pressures. The subsequent sections briefly describe how this improved performance can be achieved. The goal of this book is to provide the necessary knowledge to allow a reader to understand both the technology and business processes that underlie BIM.
Before owners engage an architect, it is necessary to determine whether a building of a given size, quality level, and desired program requirements can be built within a given cost and time budget. In other words, can a given build- ing meet the financial requirements of an owner? If these questions can be answered with relative certainty, owners can then proceed with the expecta- tion that their goals are achievable. Finding out that a particular design is
BIM, Analysis tools, IPD, Lean
Reduced time for Design and const. Reduced cost forDesign and const.
Increased complexity of design
Reduced cost for energy use
Improved building performance
Increased Pressures on the Building Process
Sustainable design & construction
Reduced construction cost and time
FIGURE 1– BIM technology and associ- ated processes can help to respond to the increasing pressures on a building over its lifecycle.
20 Chapter 1^ BIM Handbook Introduction