
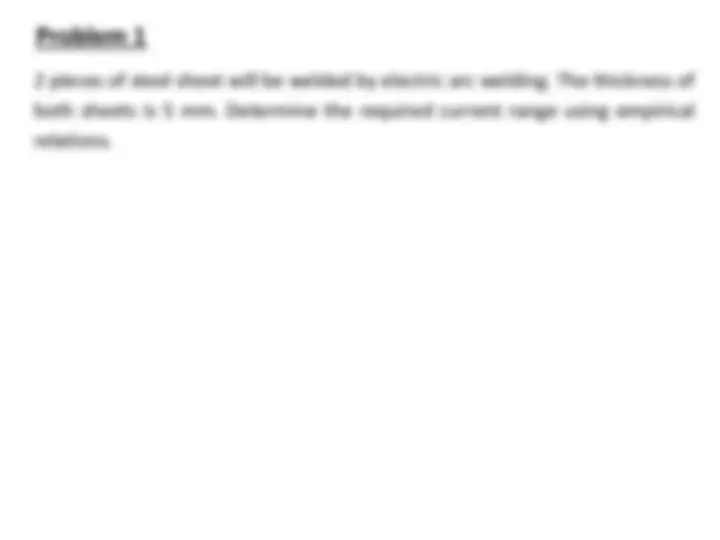
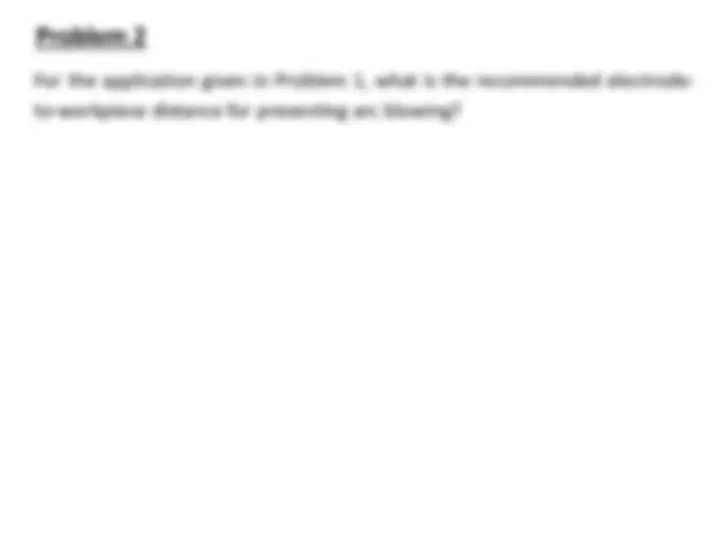
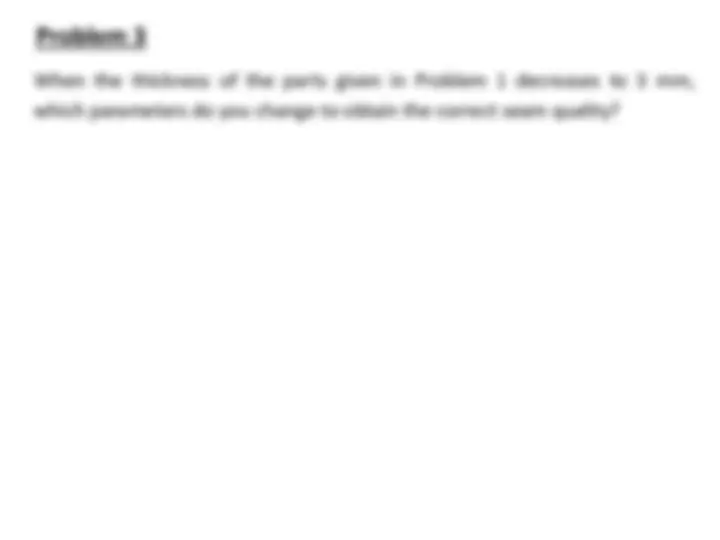
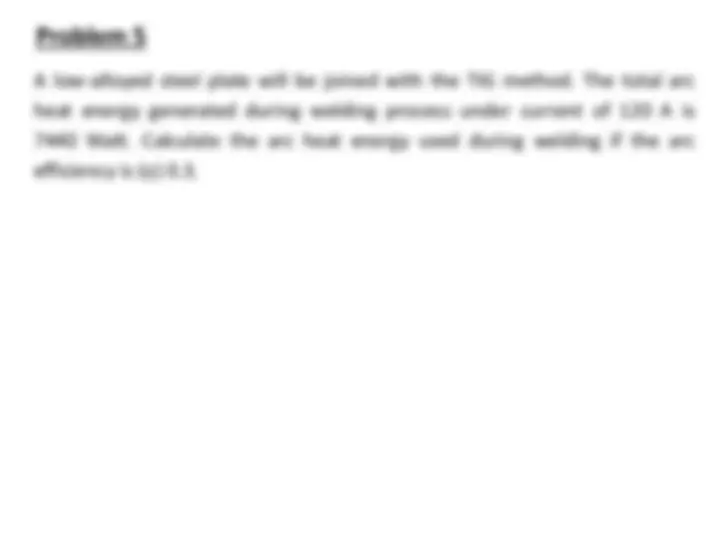
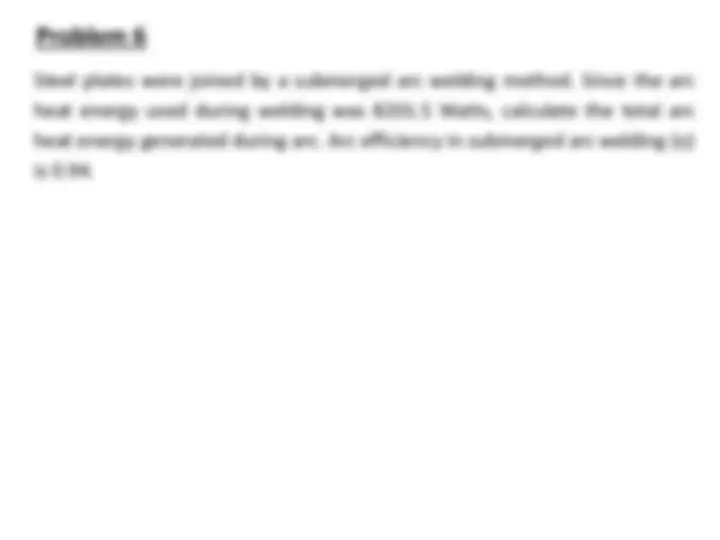
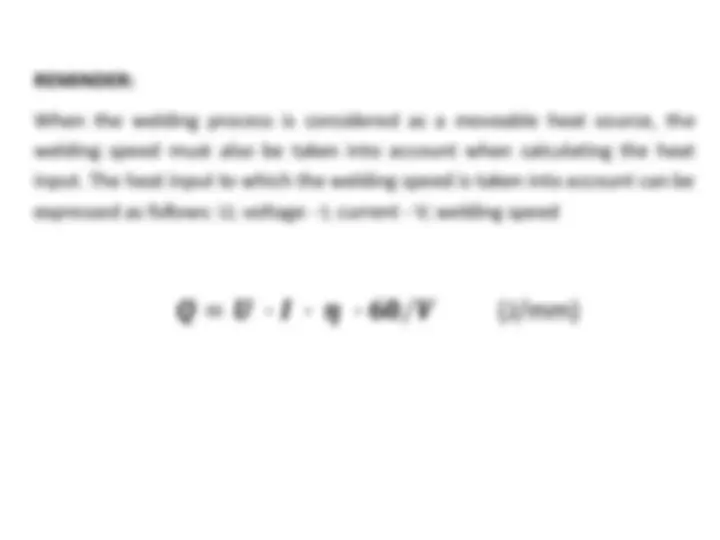
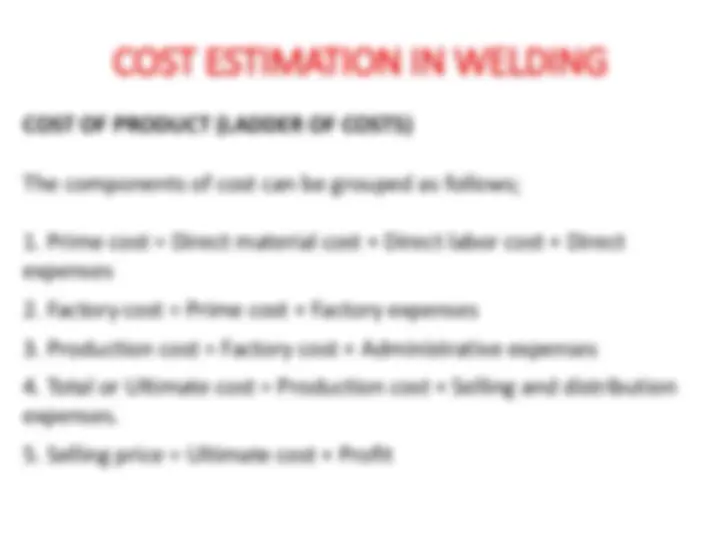
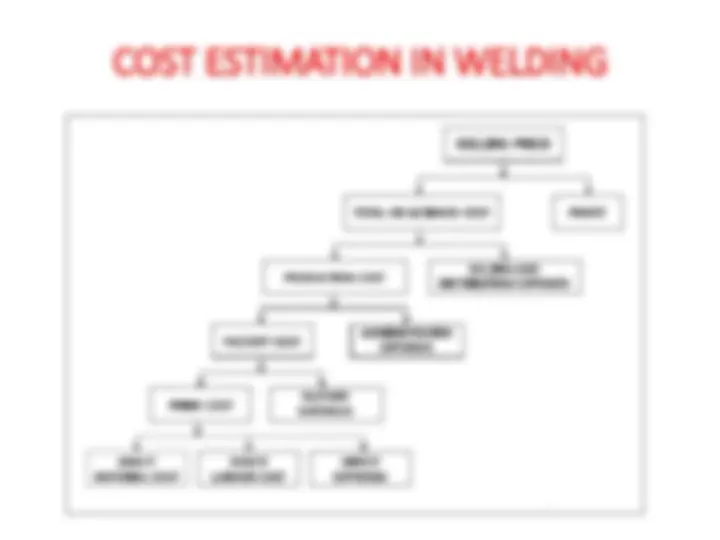
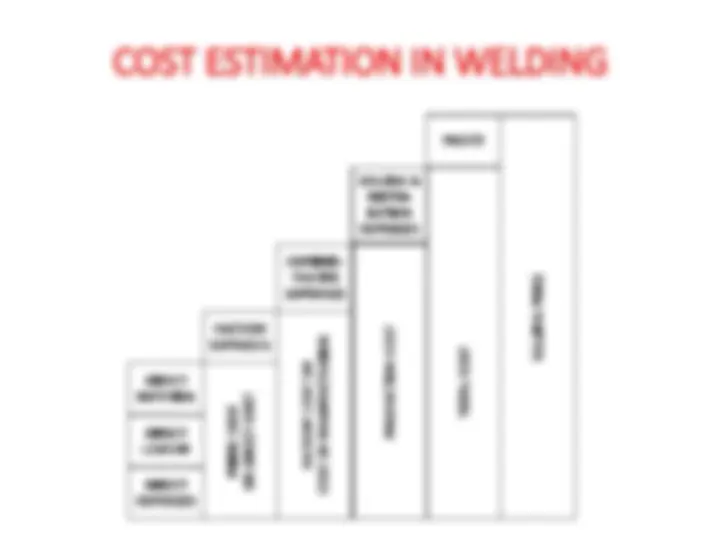
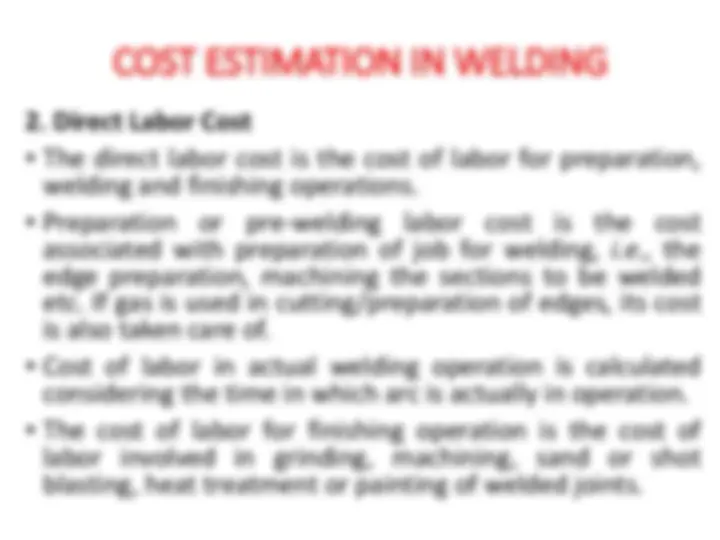
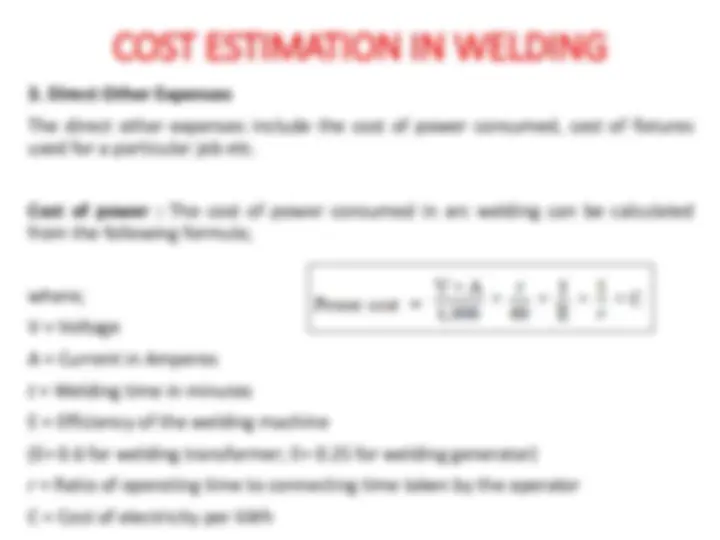
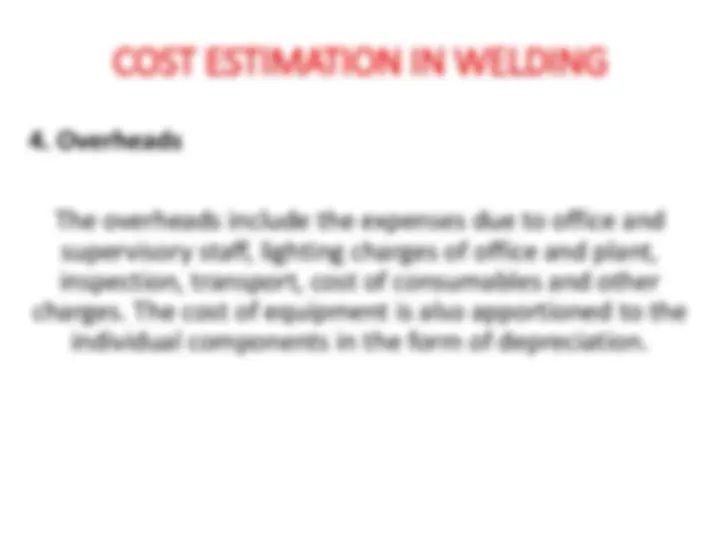
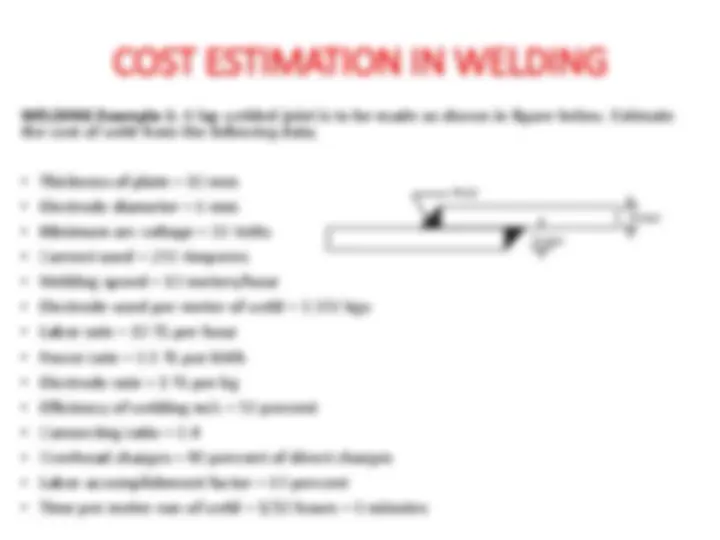
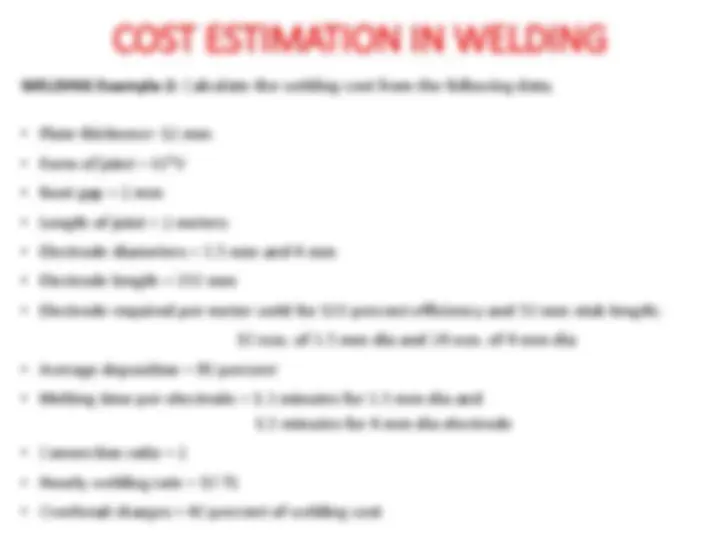
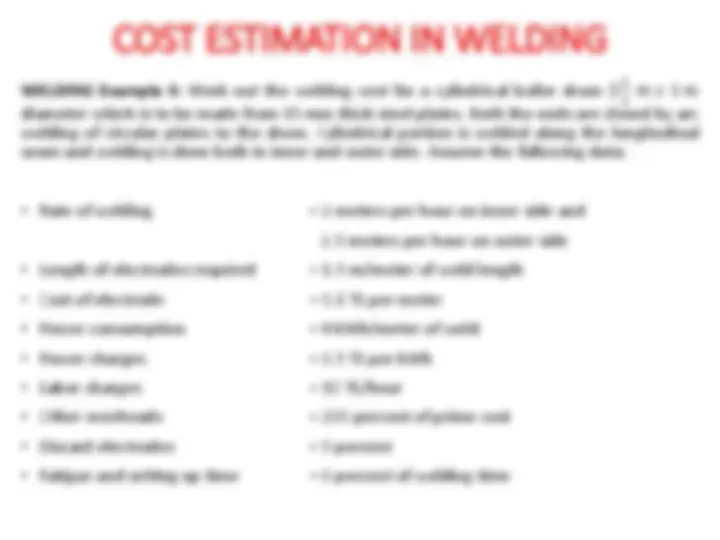
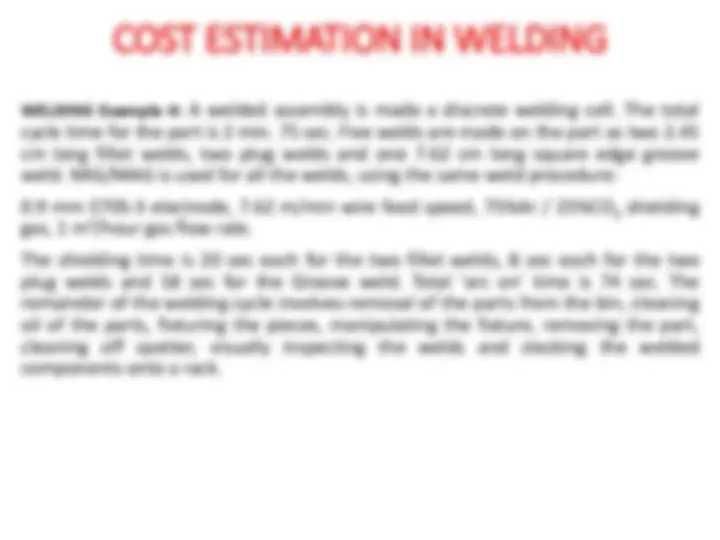
Study with the several resources on Docsity
Earn points by helping other students or get them with a premium plan
Prepare for your exams
Study with the several resources on Docsity
Earn points to download
Earn points by helping other students or get them with a premium plan
Community
Ask the community for help and clear up your study doubts
Discover the best universities in your country according to Docsity users
Free resources
Download our free guides on studying techniques, anxiety management strategies, and thesis advice from Docsity tutors
MAnu İmalat yöntemleri Yıldız tekink üniversitesi
Typology: Lecture notes
1 / 24
This page cannot be seen from the preview
Don't miss anything!
APPLICATION PROBLEMS
For the application given in Problem 1 , what is the recommended electrode- to-workpiece distance for preventing arc blowing?
When the thickness of the parts given in Problem 1 decreases to 3 mm, which parameters do you change to obtain the correct seam quality?
Low carbon steel plates will be welded by MIG method. If the welding current is 250 A and the welding voltage is 35 V in the joining process, then calculate the arc heat energy used during welding (arc efficiency ( η ) is 0. 7 )
A low-alloyed steel plate will be joined with the TIG method. The total arc heat energy generated during welding process under current of 120 A is 7440 Watt. Calculate the arc heat energy used during welding if the arc efficiency is ( η ) 0. 3.
When the welding process is considered as a moveable heat source, the welding speed must also be taken into account when calculating the heat input. The heat input to which the welding speed is taken into account can be expressed as follows: U; voltage - I; current - V; welding speed
A 2. 5 mm thick 312 austenitic stainless steel plate will be joined by TIG and plasma welding methods. In the TIG welding process, the welding current is measured at 125 A, the welding voltage is 12 V and the welding speed is 260 mm/min. In the plasma welding process, the welding current is measured as 75 A, the welding voltage is 18 V and the welding speed is 340 mm/min. Calculate the source heat input for both methods. Interpret the results. The arc efficiency for the TIG method and the plasma source will be 0. 6. Discuss HAZ.
COST ESTIMATION IN WELDING
COST ESTIMATION IN WELDING
COST ESTIMATION IN WELDING
COST ESTIMATION IN WELDING
3. Direct Other Expenses The direct other expenses include the cost of power consumed, cost of fixtures used for a particular job etc. Cost of power : The cost of power consumed in arc welding can be calculated from the following formula; where; V = Voltage A = Current in Amperes t = Welding time in minutes E = Efficiency of the welding machine (E= 0.6 for welding transformer; E= 0.25 for welding generator) r = Ratio of operating time to connecting time taken by the operator C = Cost of electricity per kWh COST ESTIMATION IN WELDING
COST ESTIMATION IN WELDING