
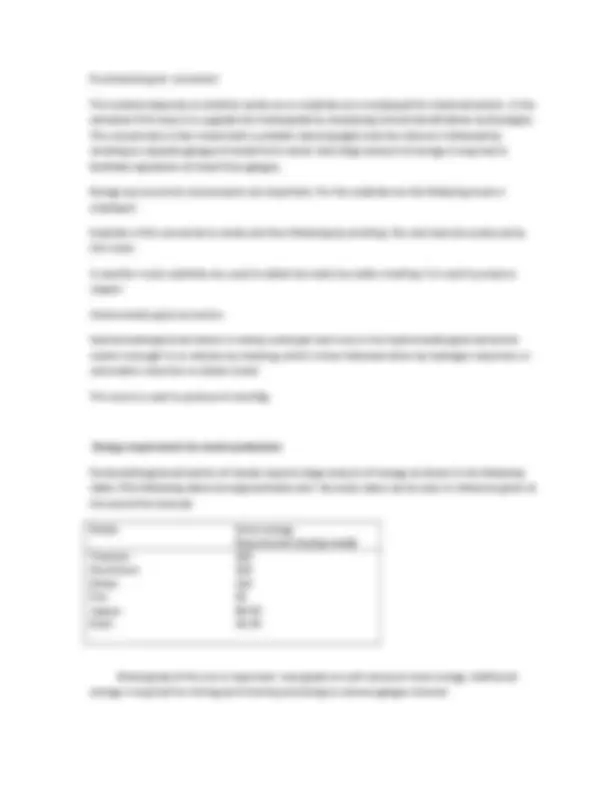
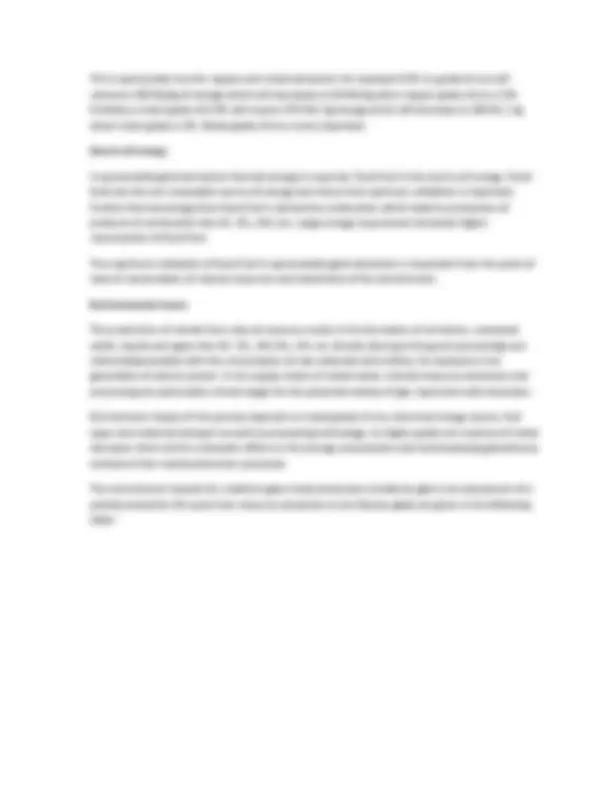
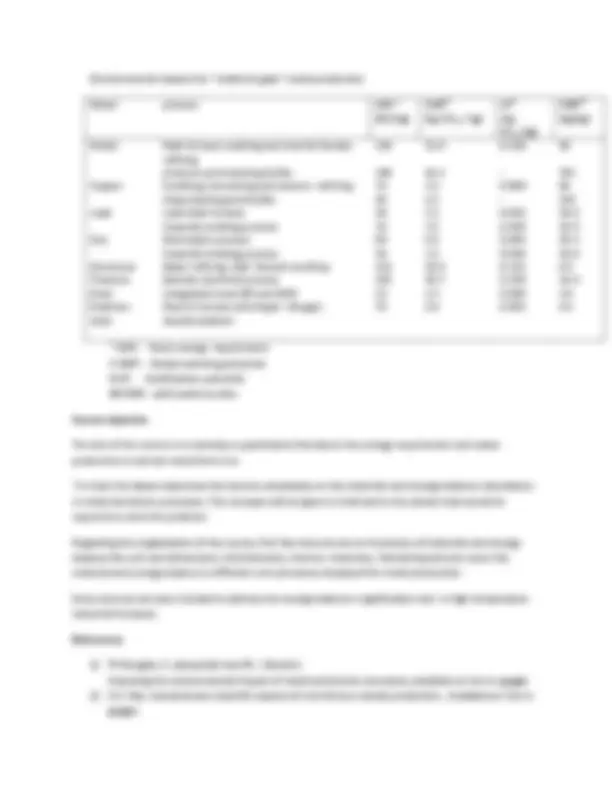
Study with the several resources on Docsity
Earn points by helping other students or get them with a premium plan
Prepare for your exams
Study with the several resources on Docsity
Earn points to download
Earn points by helping other students or get them with a premium plan
Community
Ask the community for help and clear up your study doubts
Discover the best universities in your country according to Docsity users
Free resources
Download our free guides on studying techniques, anxiety management strategies, and thesis advice from Docsity tutors
Some concept of Materials and Heat Balance in Metallurgical Processes are Blast Furnace Stoichiometry, Blast Furnace, Coke Making, Chalcopyrite Ore, Complex Sulphide Ores.Main points of this lecture are: Environmental Issues, Extraction Requirements, Metal Extraction, Energy Requirements, Environmental Issues, Course Objectives, Natural Reserves, Stoichiometric Proportion, Valuable Minerals, Sulphide Ore
Typology: Study notes
1 / 5
This page cannot be seen from the preview
Don't miss anything!
Lecture 1: introduction
Preamble
Characterization of natural reserves of metal
Metal extraction requirements
Energy requirements for metal production
Sources of energy
Environmental issues
Course objectives
References
Key words: Life cycle assessment, metal extraction, energy resources.
Preamble
Materials and heat balance of metal extraction processes constitute a very important exercise to know
the flow of materials and energy and to identify the amount of wastes produced and energy consumed.
Productions of metals from natural reserves are associated with waste production and energy
consumption.
In the future the consumption of metals is bound to increase particularly in India in order to improve its
infrastructure and standard of living of its people. An assessment of metal production processes is called
for in order to optimize the material and energy consumption to conserve the natural resources of
metals and energy. The present course on materials and heat balance is developed to keep in mind the
energy and environment issues related to metal extraction processes.
For this purpose several problems are discussed and the results are analyzed. The fundamentals of
extraction processes are discussed to the extent of their utility in problem solving. Reader may go
through the references given for the detailed description.
Characterization of natural reserves of metals
T he natural reserve of a metal is called “ore”. Ore is an aggregate of minerals. A mineral in an inorganic
compound in which elements are mixed in stoichiometric proportion, for example Al 2 O 3 is a mineral in
which 2 moles of aluminum are combined with 1.5 moles of oxygen. An ore of any metal contains
valuable mineral and gangue minerals. Valuable mineral is the mineral which is used to produce metal.
In the ore, metal grade is important.
Metal grade of an ore = A୫୭୳୬୲A୫୭୳୬୲ ୭ ୭୰ୣ.^ ୭ ୫ୣ୲ୟ୪ ୧୬ ୭୰ୣ ൈଵ
It must be noted very clearly that ore does not contain metal but metal in the ore is in the form of a
mineral. Metal grade is used to characterize an ore reserve. For example metal grade of iron in pure
Fe 2 O 3 is 70%. IF iron ore contains 80% Fe 2 O 3 , then iron grade of ore in 56%. This means that 44% of the
ore is waste both in terms of solid and oxygen of the valuable mineral. In the following table metal grade
of certain ores, valuable minerals etc. are given:
Metal Ore Valuable mineral
Metal grade (%)
Ti C Fe Ni Pb
Bauxite Ilmenite Sulphide Hematite Sulphide ore Sulphide ore
Al 2 O (^3) Ti O 2 Cu Fe S Fe 2 O 3 Ni 3 S 2 PbS
2 to 3%. 56% 64% 2.3% 5.5%
We note the following form the above table:
Metal extraction requirement:
The chemical combination of metal with sulphur or oxygen in a mineral is accompanied with high heat of
formation
Mineral Heat of formation ۛ ܪ∆ (k cal /kg mole)
Fe 2 O 3 Al 2 O 3 Cu 2 s Zns Pbs Fe 3 O 4 Ti O 2 MgO
198 x10 3 380 x10 3 19 x10 3 44 x10 3 22 x10 3 26 x10 3 218 x10 3 142 x10 3
Thus large amount of energy would be required for example to produce Fe or Al from their respective
minerals. Two basic methods of metal extraction are:
This is particularly true for copper and nickel extraction: for example 0.5% Cu grade of ore will
consume 250 Mj/kg of energy which will decreases to 50 MJ/kg when copper grade of ore is 2%.
Similarly a nickel grade of 0.5% will require 375 MJ/ kg energy which will decrease to 150 MJ / kg
when nickel grade is 2%. Metal grade of ore is very important.
Source of energy
In pyrometallurgical extraction thermal energy is required. Fossil fuel is the source of energy. Fossil
fuels are the non renewable source of energy and hence their optimum utilization is important.
Further thermal energy from fossil fuel is derived by combustion which leads to production of
products of combustion like CO, CO 2 , NOx etc. Large energy requirement demands higher
consumption of fossil fuel.
Thus optimum utilization of fossil fuel in pyrometallurgical extraction is important from the point of
view of conservation of natural resources and cleanliness of the environment.
Environmental issues
The production of metals from natural reserves results in the formation of emissions, unwanted
solids, liquids and gases like CO, CO 2 , NOx SO 2 , SO 3 etc directly (during mining and processing) and
indirectly(associated with the consumption of raw materials and utilities, for example in the
generation of electric power. In the supply chains of metal needs, mineral resource extraction and
processing are particularly critical stages for the potential release of gas, liquid and solid emissions.
Environment impact of the process depends on metal grade of ore, electrical energy source, fuel
types and material transport as well as processing technology. As higher grade ore reserves of metal
decrease, there will be a dramatic effect on the energy consumption and accompanying greenhouse
emissions from metal production processes.
The environment impacts for cradle‐to‐gate metal production (cradle‐to‐gate is an assessment of a
partial production life cycle from resource extraction to the factory gate) are given in the following
table:
Environmental impacts for “cradle‐to‐gate” metal production
Metal process GER * (MJ/kg)
(kg CO2e / kg)
(kg SO2e/kg)
(kg/kg)
Nickel
Copper
Lead
Zinc
Aluminum Titanium Steel Stainless steel
flash furnace smelting and sherritt Gordon refining pressure acid leaching Sx/Ew Smelting /converting and electro –refining Heap leaching and Sx/Ew Lead blast furnace Imperial smelting process Electrolytic process Imperial smelting process Bayer refining ,Hall‐ Heroult smelting Beecher and Kroll process Integrated route (BF and BOF) Electric furnace and Argon –Oxygen decarburization
Course objective
The aim of the course is to develop a quantitative feel about the energy requirement and waste
production to extract metal form ore.
To meet the above objectives the lectures emphasize on the materials and energy balance calculations
in metal extraction processes. The concepts will be given in brief and to the extent that would be
required to solve the problem.
Regarding the organization of the course, first few lectures are on the basics of materials and energy
balance like unit and dimensions, stoichiometry, thermo‐ chemistry. Remaining lectures cover the
material and energy balance in different unit processes employed for metal production.
Some lectures are also included to address the energy balance in gasification and in high temperature
industrial furnaces.
References